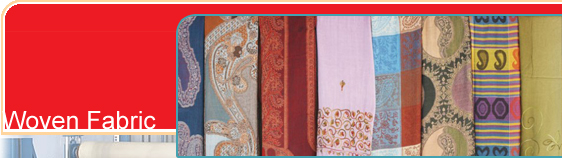
Mercerisers
Mercerising can be done at different stages during the pre-treatment process. This could be after Desizing or after Scouring or after Bleaching. When done after desize-washing, it induces maximum lustre onto the fabric. However, contamination of lye can occur, which reduces life of the caustic lye. High degree of whiteness can be achieved if the bleaching process is done after mercerisation. Mercerisation after scouring and bleaching prevents contamination of caustic lye but effects the whiteness and absorbency. Mercerising can be done either on wet fabric with a lye concentration controller or on dry fabrics. Mercerising could be done with either cold lye or with hot caustic.
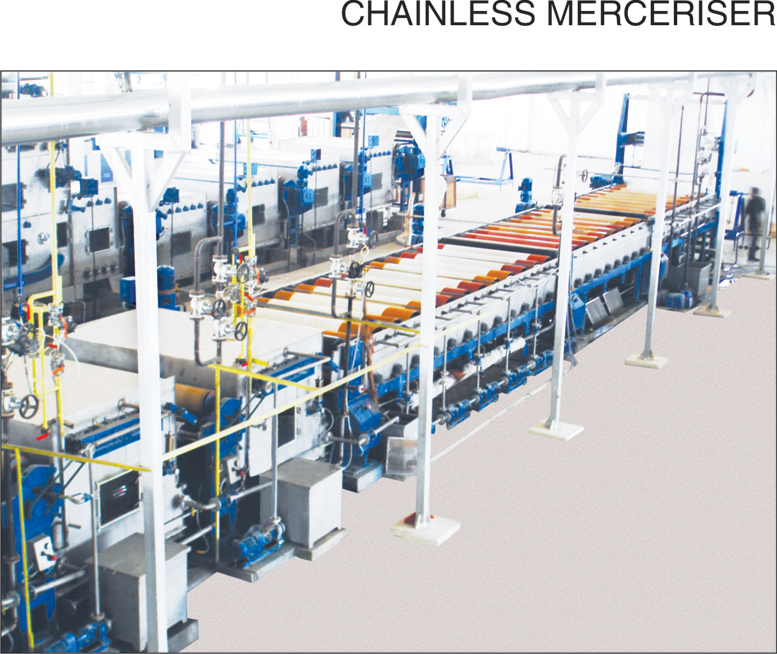
FABRIC FEEDING
Fabric feeding through Guiding and Centering devices. Positively Driven Batching-off unit with / without J scray for low tension and continuous working. Combination of three individually easily adjustable Curved Bar Rubber Expanders to feed Fabric in stretched condition.
LYE IMPREGNATOR
Made from Stainless Steel unless otherwise specified. Caustic lye impregnation with rollers dipped in lye as well as by caustic filled nips formed between top and bottom rollers. Grooved Bottom Rollers for better width stability. Dwell time control by speed adjustments. Driven rollers at regular intervals can be supplied for tension control. Can be equipped with chiller / heater for lye temperature control. Equipped with automatic / manual continuous filtering arrangement. Automatic fresh lye addition to maintain uniform caustic lye consistency to pre-adjusted concentration.
IMPREGNATOR WITH DWELL ZONE
Mercerisers Model M-10 and above have the Impregnating zone subdivided into a Impregnating zone and a Dwell Zone. It is possible to use caustic lye in all sections or use caustic lye in the first Impregnator and use the second as a dwelling zone. For specific fabric tension requirements, drive to the intermediate bottom rollers can be provided to reduce tension in the fabric under process, ensuring better control on width.
TENSION CONTROLLED DRIVE
Facility to over-feed fabrics to ensure better width stability. Programmable / pre-set speed between various individual drives. Multi-point Variable Frequency Drive with encoders to maintain uniform tension. Constant fabric tension.
STABILISER
Excellent cascading throughout the passage in Stabiliser. Intensive Neutralisation with the help of fast liquor circulation in each cascade. Grooved Bottom Rollers for better width stability. Precise temperature control near boiling point guarantees best caustic removal from fabric. Excellent dimensional stability after stabiliser. Constant and uniform concentration of overflowing wash liquor.
SQUEEZING AFTER IMPREGNATOR / STABILISER
Nip formed with Wear resistant Stainless Steel / Ebonite roller and special Rubber Roller for excellent caustic removal and longer life. Adjustable nip pressure upto 30-50 kg-cm. Automatic opening of nip when machine stops. Drive through direct-coupled Motor-Gearbox with Variable Frequency Drives.
WASHING
SQUEEZING AFTER WASHING
LIQUOR CIRCULATION
A suitable pump with a filtering arrangement is provided in the Impregnator, which delivers the filtered caustic lye back into the Impregnator through a distribution system located between each Roller. On request, the machine can be equipped with a continuous auto cleaning filter. The stabiliser is compartmentalised and each compartment is provided with a Stainless Steel Pump which collects the hot wash liquor from the first washing compartment and pumps it to the last section of the stabiliser. This liquor is spread onto the fabric. Similarly from this last section, the liquor is collected, filtered and pumped to the preceding section. This continues till the first stabilising section, where the accumulated liquor is taken for recovery / disposal. The flow of liquor in the direction opposite to the movement of the fabric ensures excellent removal of caustic.

SALIENT FEATURES
- Modular design, tailored to suit individual requirements
- Grooved Bottom Rollers for better width stability
- Low width shrinkage with excellent dimensional stability
- Mercerised fabric has excellent lustre, high absorbency, better handle, uniform and repeatable finishing results
- Can be equi pped with PLC controls for different functions such as fabric tension in Impregnator and Stabiliser, Shrinkage-Controller-cum Indicator etc. pH Indication / Control at the end of Washing, dwell time control by controlling speed flow control for walls & NaOH concentration control etc.
- Lower Lye, Water and Steam Consumption
- Low maintainance
- Lower incidence of re-dyeing

Singening System
SWASTIK Singeing Machines are designed to obtain different singeing effects such as Hard singeing – Medium singeing – Soft singeing to suit all kinds of fabric processing. This is achieved by adjusting the guide roller positions with respect to the flame.
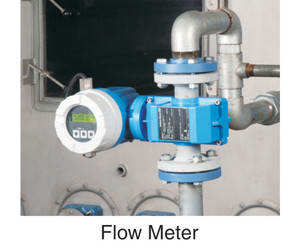
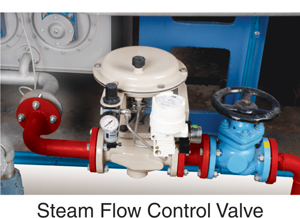
ACCESSORIES WET-ON-WET
The SWASTIK Merceriser can be provided with a NaOH preparation tank, chilling arrangement for the lye and a caustic recovery plant, if required. The machine can be supplied with acid neutralization system in the washer and a Dryer.
WET-ON-WET MERCERISING
Desize Impregnated Fabric can be Mercerised right away in our Wet-on-Wet Merceriser WWM-X. The number of Washing
Compartments depends upon the quality of fabric and the production required. In cases where the fabric is Mercerised after Scouring, Wet-on-Wet mercerising is possible using only one Pre-wash Tank. Washing after mercerising remains standard. A heavy duty Squeeze Nip “Hi-Squeeze” with anti-deflection roller prior to the Impregnator enables uniform mercerising results. Impregnator for Wet-on-Wet Merceriser is equipped with an automatic Lye concentration controller.
HOT MERCERISING
Being a cost effective measure, the tendency to use Hot Mercerising is on the increase in recent years. Hot Caustic lye (at about 60°C) penetrates better and more evenly to the yarn core (of the fabrics). Swelling is better as compared to cold Mercerising which helps to improve the dimensional stability of fabrics. Hot Mercerising ensures even Dye penetration and imparts a softer handle and better appearance. Shorter impregnation time requirement reduces investment cost. For Hot Mercerising, the Impregnating section is equipped with an indirect steam heating system with a temperature controller to maintain uniform temperature.
THE COLD IMPREGNATION PROCESS
The traditional cold impregnation process imparts more lustre to the fibre than the hot impregnation system mainly due to the greater shrinkage and high tensions needed the re-stretch the fabric to the desired width.
WIDTH STABILITY
can be achieved by differential speed setting of the squeezing units, controlling the shrinkage or elongation of the fabric. This can be done manually or through automation, using PLC.
COMBINED CHAIN AND CHAINLESS MERCERISER
Besides Lustre, Depth of Colour and fabric feel, dimensional stability of the fabric is the most essential objective of mercerization today. These can be fulfilled with the Combined Chain and Chainless Merceriser. The length and width of the fabric can be controlled at will (within physical limits) using the combination of Chainless driven rollers with fully controlled drive and a stenter frame. The layout of the machine is shown in the layout drawing below. The intensive impregnating zone is followed by a reaction zone. Up to this point the fabric guidance is on the chainless princi ple. A part of the stabilizing zone is a stenter section using the pin chain princi ple. Final stabilization compartment is again chainless and is followed by the normal high-efficiency washing and neutralizing compartments. In the Stabilizing Zone, the uniformly applied lye is removed. Hot weak lye is first sprayed onto the fabric. Gradually reducing the shrinking force. In this condition the fabric can be stretched to the desired width with a comparatively less force. The possibility of stretching on the stenter ensures uniform shrinkage and even distance between warp yarn from the selvedge to the center. This is an important advantage of the Combined Chain and Chainless Merceriser if dyed woven or striped fabrics are to be processed. Increase in fabric width can also be achieved. The pin chain permits stretching by increasing the speed or shrinkage through fabric overfeed.
AUTOMATION
SWASTIK offers a fully automated machine with the most modern PLC control system which ensures optimum production. The level of automation can be designed for specific requirements of individual customers. Typical level of automation to access and control basic machine parameters, functions and displays using PLC with Graphic Colour Screen Display of various functions on a Touch Screen, can be as follows:
- Drive synchronisation
- Automatic Speed Control of machine through programmed Dwell time
- Lye Dosing and concentration control as per set parameters
- Liquor/Water Flow proportionate to fabric weight
- Level control
- Temperature control
- Fabric Tension control by overfeeding in the Impregnator and Stabiliser
- Acid Dosing with pH control.
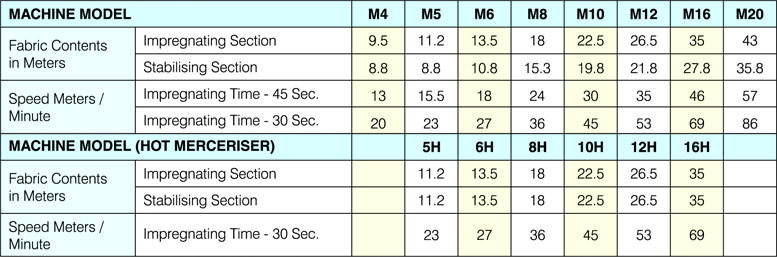
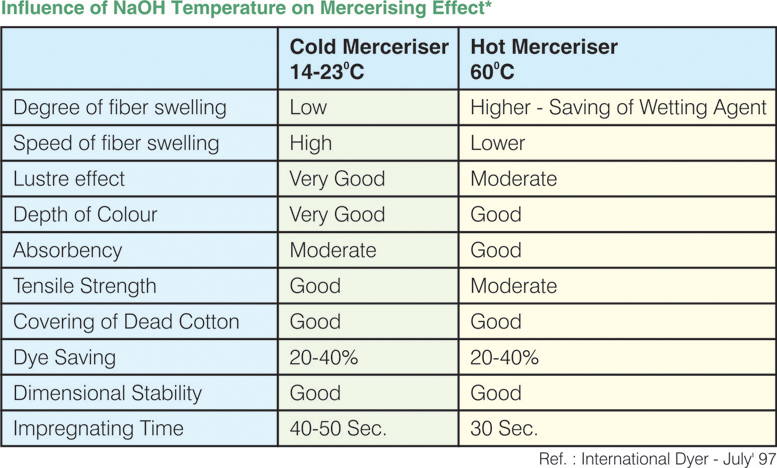