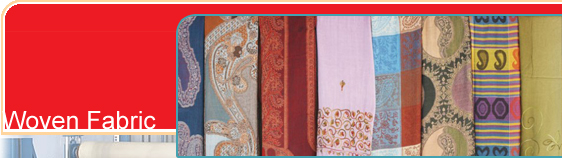
Compressive Shrinking Ranges
The SWASTIK COMPRESSIVE SHRINKING RANGE SF-Super-Shrinkspan> is designed to achieve Shrinking results in accordance with international standards for the dimensional stability of fabrics, for widths upto 3600 mm. Fabric is shrunk between the Rubber Belt and the hot mirror-polished drum by adjusting the belt stretch by acting on the pressure roller. Once the Belt leaves the pressure roller, it contracts the fabric between the rubber belt and the mirror finish heated drum and is shrunk. Shrinkage variation is obtained by varying the pressure applied to the rubber belt. To permit the required contraction, the fabric should be properly guided over the belt. Greater the Pressure – higher the shrinkage. Good and even Damping is a pre-requisite for achieving required shrinking results.
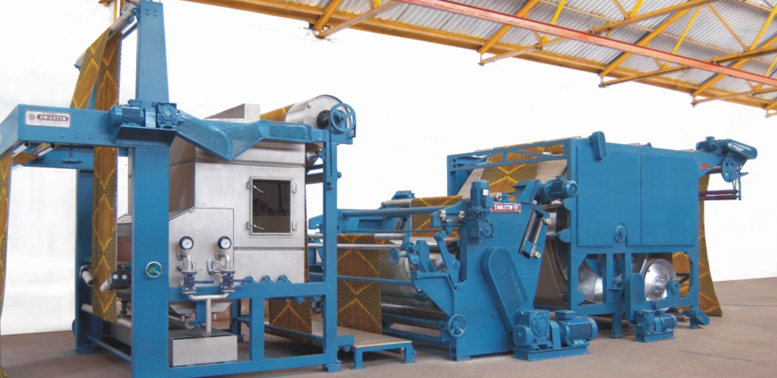
Fabric Feeding
with Tension bars and or a swiveling tension device with or without positive draw nip; cloth guiders; necessary guide rollers; a measuring / metering roller and a compensator. The machine can be equipped with a pneumatically operated, positively driven Unwinding Device with AC Inverter Drive, with stainless steel Scray for continuous operations. A light draw Nip is provided to lay the fabric in the scray. A three rollers pneumatically operated centering device can be incorporated on request.
Damping
DAMPING : A perforated stainless steel drum of diameter 568 mm filled with steam and covered with a special felt cloth, is used to damp fabrics before the rubber belt unit. Optionally, a rotor damping unit can be installed in addition to the damping unit.
The unit can be shifted backwards on rails for belt grinding work, when required.
To ensure required shrinkage, a device consisting of a free roll and a scroll roll is provided to feed the fabric to the Rubber belt unit at the required position.
The unit can be shifted backwards on rails for belt grinding work, when required.
To ensure required shrinkage, a device consisting of a free roll and a scroll roll is provided to feed the fabric to the Rubber belt unit at the required position.

Shrinking Unit
consists of a main heated and mirror polished cylinder running in roller bearings. Tension Roller, Pressure Roller and guide rollers running free on bearings. Both the tension roller and the pressure roller can be adjusted manually / electrically with the help of special motors as desired.
Suitably designed mechanically / pneumatically operated rubber belt squeezing rollers ensure longer life of the belt. Special care is taken to ensure longer
The Rubber Belt Cooling device consists of a water spraying arrangement on both faces of the rubber belt. Water cooling, filtering and re-circulating device with help of a pump can be supplied optionally.
The Rubber Belt unit is equipped with a dynamically balanced, adjustable belt grinding roller. The machine can be equipped with a suction device for dust removal from the belt grinding device on request.
Suitably designed mechanically / pneumatically operated rubber belt squeezing rollers ensure longer life of the belt. Special care is taken to ensure longer
The Rubber Belt Cooling device consists of a water spraying arrangement on both faces of the rubber belt. Water cooling, filtering and re-circulating device with help of a pump can be supplied optionally.
The Rubber Belt unit is equipped with a dynamically balanced, adjustable belt grinding roller. The machine can be equipped with a suction device for dust removal from the belt grinding device on request.
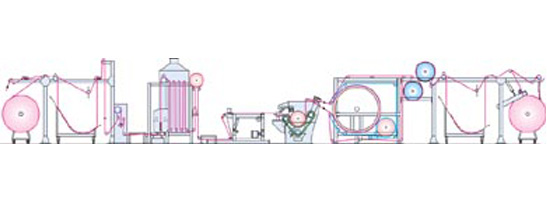
Palmer Unit
can be equipped with the Main Drum of either flanged – end or jacketed construction, in different diameters -1500 mm, 1800 mm, 1950 mm, 2500 mm and in widths up to 3800 mm. Palmer unit can be operated in either direction to finish either side of the fabric. Felt Drying cylinder is of Ø780 mm. For Denim Finishing Ranges with Ø2500 mm Palmer
A suitable woollen / synthetic superfine quality felt ensures excellent fabric finish. Felt Centering Device is pneumatic / motorized and tensioning device is mechanically or pneumatically operated. Hard Chrome plated guide rollers are provided for felt guiding and cloth guide rollers are in stainless steel.
A suitable woollen / synthetic superfine quality felt ensures excellent fabric finish. Felt Centering Device is pneumatic / motorized and tensioning device is mechanically or pneumatically operated. Hard Chrome plated guide rollers are provided for felt guiding and cloth guide rollers are in stainless steel.
Cooling Cylinder
One, two or three stainless steel jacketed cylinders can be fitted for chilled water circulation to cool the hot fabric as it comes out of the Palmer unit.
Delivery Unit
Consists of Pneumatically operated, AC Inverter controlled positively driven Big Batching arrangement and a Plaiting device. A Stainless Steel scray can be supplied for continuous operation.

Special Finishing Range
Compressive Shrinking Range with
Damping & Steaming Unit
- Tension Bar.
- Swivel Tension Unit.
- Damping Cylinder.
- Shrinking Cylinder.
- Belt Pressure Roll.
- Belt Tension Roll.
- Water Removal Rolls.
- Trough Roll
- Felt Cylinder.
- Plaiter Roll.
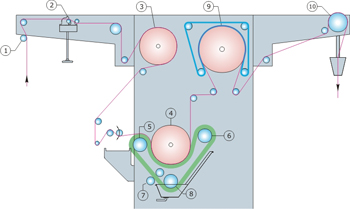
Special finishing range
SWASTIK also offers a compact Shrinking Range to finish delicate woven and knitted fabrics in open form. The machine consists of a steam damping arrangement; rubber belt shrinking unit and a small felt finishing unit with a special feeding and delivery arrangements to take care of the needs of delicate and knit fabrics.
Automation
Indicator and Controller. The machine is provided with two nos. fabric measuring systems, one after Damping and 2nd one before Plaiter, with a PLC. Shrinkage is measured and controlled by acting on the motor of the pressure roller, which will automatically increase or decrease the pressure as required.
“Super Shrink” can also be provided with temperature and pressure controller for the steam heated cylinder of Rubber Belt and Palmer, and a Humidity Indicator for the damping unit.
“Super Shrink” can also be provided with temperature and pressure controller for the steam heated cylinder of Rubber Belt and Palmer, and a Humidity Indicator for the damping unit.